The waiting game in IT hardware maintenance
Addressing the race against time in parts availability issues.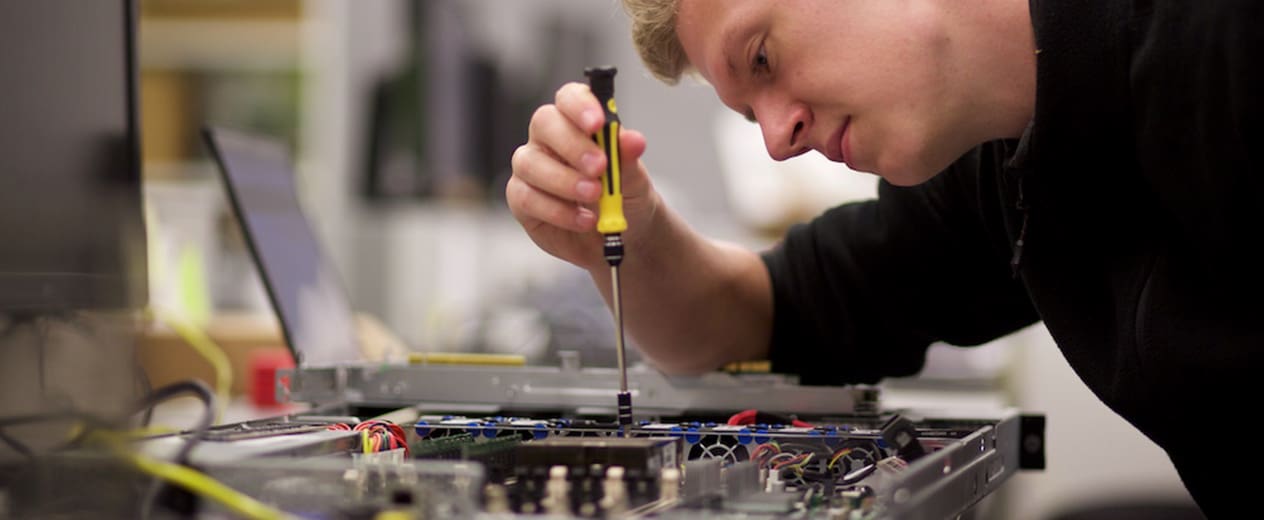
Adoption, migration, optimisation, security and management services designed to deliver business agility.
Improve your security posture with tailored strategies and front-line defence services.
Scalable colocation and connectivity within a hyper secure environment.
Disaster recovery and serviced offices in secure, premium office facilities.
Tailored end-to-end solutions for your hardware ecosystem across the widest range of vendors.
Seamless management of your IT environment, underpinned by world-class cyber security, no matter where you are on your journey.
Securely and effectively operate, monitor and maintain your network.
Enjoy the comfort of a modern working space supported by world class technology, security and resilience.
Help your clients take control of their IT environment with Australia and New Zealand’s leading hardware maintenance provider.
Interactive Anywhere provides robust infrastructure solutions designed to support the seamless operation of digital environments. These solutions include scalable cloud services, reliable data storage, and efficient server management, ensuring optimal performance and uptime.
The network solutions from Interactive Anywhere encompass comprehensive design, implementation, and maintenance of secure and efficient networks. By optimising connectivity and bandwidth, these solutions facilitate seamless communication and data transfer, enhancing overall productivity and operational efficiency.
Interactive Anywhere offers dedicated end user support services that ensure users receive prompt assistance with technical issues. This includes help desk support, troubleshooting, and training, aimed at improving user experience and minimising downtime for businesses.
With a focus on safeguarding digital assets, Interactive Anywhere's cyber security solutions provide advanced protection against cyber threats. These solutions include threat detection, risk management, and compliance services, ensuring businesses can operate securely and with confidence.
Interactive offers financial institutions with secure operations, robust cyber security, seamless connectivity, end-user support, and cloud solutions, ensuring long-term resilience.
For manufacturing, precision and efficiency are paramount. Our solutions optimise operations, streamline processes, and ensure seamless connectivity to drive productivity and innovation.
In professional services, reliability and agility are crucial. Our solutions enhance efficiency, streamline workflows, and provide seamless connectivity, empowering firms to deliver exceptional client experiences and stay ahead in a dynamic market.
In aged care, precision and patient well-being are fundamental. Our solutions enhance operational efficiency, streamline workflows, and guarantee secure, seamless connectivity, empowering providers to deliver exceptional care and lead in an ever-evolving sector.
We're Australia's leading IT service provider and we keep technology human.
News & insights from our experts to help you drive performance and grow your business.
As an IT professional, dealing with hardware maintenance can be a race against time. It starts when a critical piece of equipment fails unexpectedly. You immediately reach out to your maintenance provider, only to find out the specific part you need isn’t available. As you wait for them to procure and deliver the part, the problems start to multiply, disrupting your organisation’s operations.
The situation becomes even more complicated when your IT systems are spread across different locations. In this blog, we’re diving into the intricate problem of part availability, examining its causes, and exploring potential solutions to combat it.
The primary issue with delays doesn’t just stem from the multitude of global suppliers, manufacturers, and distributors in the IT hardware parts supply chain. These complexities are just the tip of the iceberg. What lies beneath the surface is a deeper problem – the lack of readily available parts at the local level.
This issue is attributed to Original Equipment Manufacturers (OEMs) often not having local storage facilities. Maintaining such inventories is deemed inefficient by these companies, primarily due to high costs and management overheads. This lack of local parts availability means that even the slightest disruptions on a global or local scale can significantly slow down the delivery of essential components, exacerbating the problem.
Part delays intensify business disruption, particularly when they need to come from afar. Consider a scenario where a retail chain in regional Australia experiences a critical server failure. The essential replacement part is, however, in an OEM warehouse in Singapore.
Starting with long waiting times over the phone to escalate the issue with the OEM, the time consumed to then identify the issue, source the part, and then ship it across the continents isn’t merely inconvenient — it poses a significant threat to business continuity. The issue worsens when the part needs to be transported from Sydney to a regional location, leading to additional delays and wasted man-hours.
The ripple effects of these delays are substantial. When a crucial piece of hardware fails, everything grinds to a halt, and the financial losses begin to mount. Every minute without the part worsens the situation, affecting customer satisfaction, operational efficiency, and financial health.
A manufacturer can lose $22,000 per minute when production stops, and unplanned downtime can cost industrial manufacturers up to $50 billion every year. If you’re an IT professional, these are the numbers you dread. The significant repercussions of a typical downtime include:
In the face of these challenges, a proactive approach is essential. This includes strategic planning, effective logistics management, and maintaining a ready inventory of spare parts. The speed at which you react can also be a game-changer when issues arise, aiding your business and alleviating stress for your IT teams.
Here’s the good news: The IT maintenance industry is constantly evolving, aiming to make solutions more accessible no matter where the problem arises. With the right solutions and a partner understanding your unique needs, the waiting game in hardware maintenance could become a thing of the past.
We are the people behind the technology. We help organisations reach their full technology potential and transform. Interactive is a technology solutions provider across Australia and New Zealand providing services across three core capabilities: cloud, cyber and systems.